Functional Safety in Industry: Thinking Outside the Cage
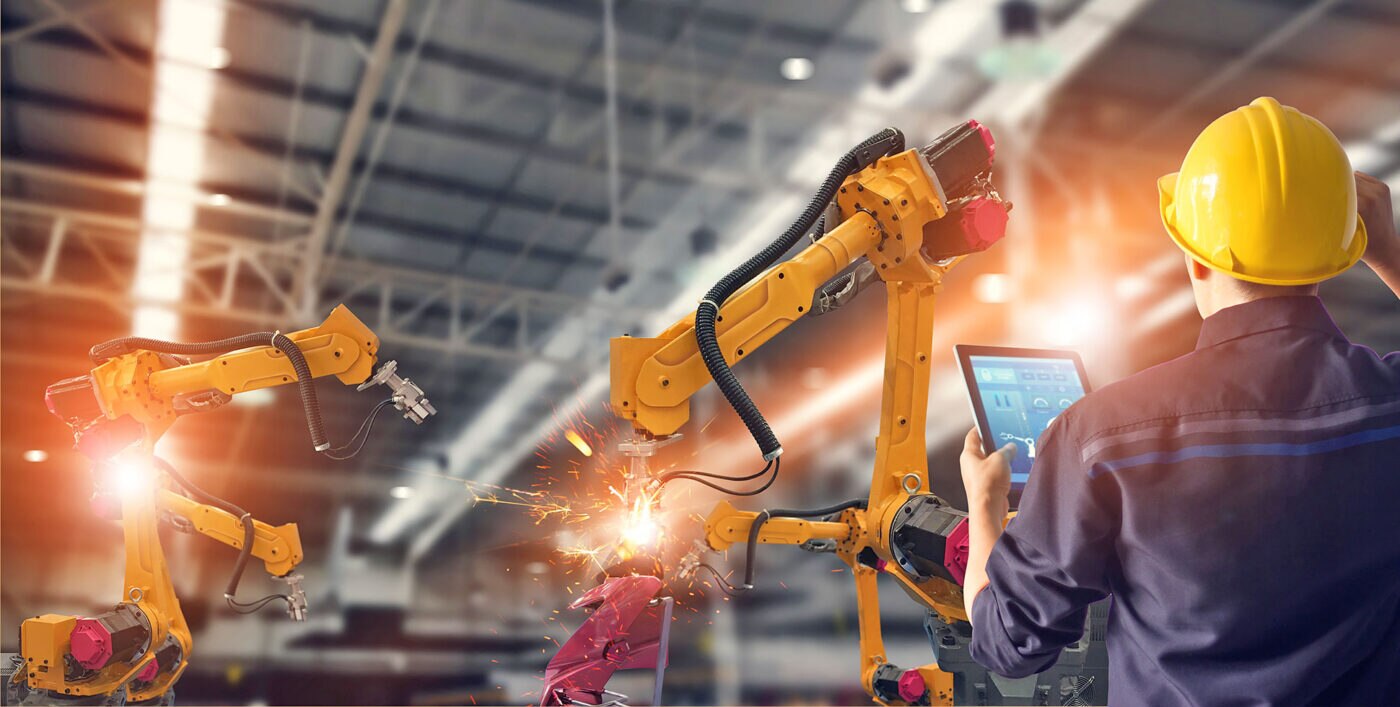
Industrial manufacture is inarguably safer than it used to be. In the United Kingdom, the Health and Safety Executive (HSE) reports an 84 percent reduction in fatal injuries within the workplace since 1974.
While part of this reduction is undoubtedly due to more robust training and regulation, the automation of potentially hazardous machinery is surely a key factor. Fundamental to this is electronic control technology, supplying the central intelligence to control a wide range of machinery from robotic arms to heavy duty metal bending presses without the need for a human operator.
Yet humans still play a vital role in any manufacturing environment, and many of today’s machines operate in close proximity to humans. Functional safety is therefore a critical element for any system deployed within a robot, factory or vehicle and is the system’s ability to detect, diagnose, and safely mitigate the occurrence of any fault, preventing harm to people and the environment.
Functional safety at its most basic
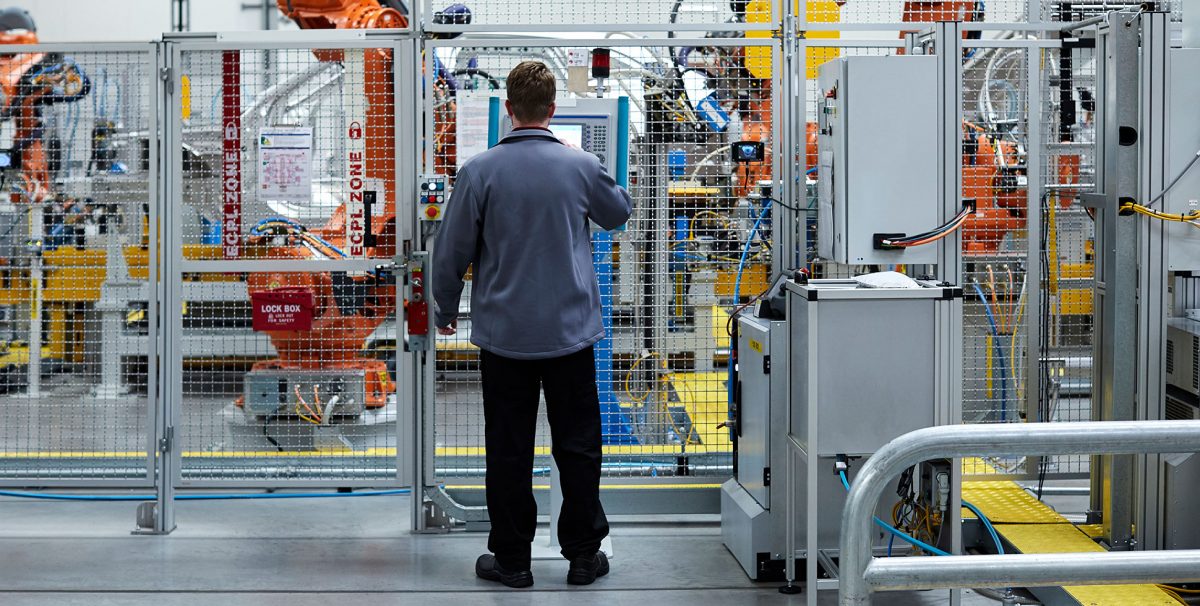
Traditionally, hazardous machines are isolated within a metal cage to distance them from their surroundings and—most importantly—from people. When the cage door is opened, the machine shuts off. This is functional safety at its most basic.
Yet a cage can take up an area of floor space far greater than the machine contained within it. With floor space a premium in many factories, fewer robots could mean reduced efficiency resulting in a negative effect on the factory’s performance.
But recent advances in functional safety may offer an alternative solution to lock and key. By implementing key safety technologies, robots could be uncaged, allowing “co-robots” to work alongside humans on a production line.
This collaborative approach to manufacturing allows the robot to take care of repetitive and mundane tasks, leaving the human to focus on critical thinking and more complex decision-making elements of the production line. However, safety is even more critical with man and machine working in such close proximity and control systems must constantly monitor the integrity of the robot and react appropriately under error conditions. This drives the need for functional safety.
For example, a co-robot has a number of sensors that can detect resistance to motion— perhaps the human is reaching across the path of the robot. In this situation, the machine should of course ‘back off’. However, if this particular system were to fail, the robot may continue its task—resulting in potential injury. This highlights the need for functional safety that designs with these cases in mind and reduces the associated risk by ensuring that any systems are monitored for correct operation and any problems are suitably diagnosed and reported.
Functional safety starts at the IP level
Conforming to safety standards is a vital step in solving the problems of deploying safety efficiently in industrial applications. Arm processors already power a broad range of applications throughout modern factories across a range of use cases from small sensors and actuators to complex robots and vision systems. Arm therefore has a robust process in place for ensuring our products conform to safety standards, including third-party assessment.
Arm Safety Ready products meet the IEC61508 standard for industrial applications, and supporting collateral is made available to all partners using Arm IP to build safe devices. Our functional safety support scales across this range of processors and also into other IP such as interconnect, interrupt controllers and memory management units.
But functional safety is not just about the hardware: software plays an important role. A reliable software toolchain, containing Software Test Libraries (STLs)—sets of tests that can be run at start-up or during operation of a system to check the processor’s internal logic—is vital to developing a functionally safe device. Arm’s toolchain contains STLs as well as a safety qualified compiler and certified code libraries to help software developers design a functionally safe system.
With the cages removed, companies looking to design products for the factory environment need to be sure that the IP they choose meets stringent functional safety criteria, whether developing a tiny sensor or robot handling dangerous materials. Whatever the application, OEMs need to be able to provide the right kinds of products for the right applications, both safe and non-safe, with the ability to scale efficiently across both.
Discover more about Arm functional safety technology and the Arm IP available in our Safety Ready portfolio
Any re-use permitted for informational and non-commercial or personal use only.