Beyond Silicon: The Future of Flexible Chips
Summary
In the past 50 years, microprocessor technology has moved from silicon capable of simple arithmetic calculations to 64-bit microprocessors that power the world’s most efficient supercomputers. And while the number of transistors has jumped from thousands to tens of billions, the materials used in chip production have remained the same. But are silicon chips the best solution for all use cases? PragmatIC believe otherwise, and their flexible chip technology suggests they may have an alternative to transform many products and markets.
In this episode, Geof Wheelwright is joined by PragmatIC CEO Scott White and James Myers, Distinguished Engineer at Arm Research. The pair will discuss the benefits and challenges of flexible chip technology, the collaborative projects between the companies and where they see the technology deployed in the future.
Additional resources:
Article (Nature): A natively flexible 32-bit Arm microprocessor (Nature)
Blog: Realizing the Full Potential of the Internet of Things
Speakers
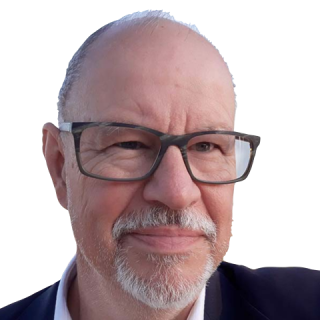
Geof Wheelwright, Arm Viewpoints Host
Geof has worked as a journalist, author, broadcaster and consultant for more than three decades – and in a variety of technical content management, corporate communications and senior management roles at several technology companies. He has contributed to a broad range of media outlets – including The Guardian, the Financial Times, The Daily Telegraph, The Daily Mail, The Independent, Canada’s National Post, Time Magazine, Newsweek and a number of specialist technology industry sites (such as Geekwire) and Travel titles (including Travel + Leisure).
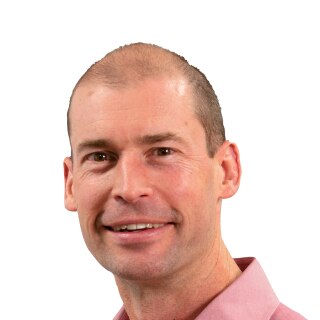
Scott White, Chief Executive Officer, PragmatIC
Scott White is an experienced serial entrepreneur, leading his sixth technology venture as CEO of PragmatIC. He was also a co-founder and board director at computer vision-based AI company Cortexica, acquired by Zebra Technologies. Past successes include Azea Networks, which he grew from concept to 8 figure sales levels before acquisition. He has lived and worked across the globe including Australia, Japan, Singapore, Indonesia, the US and UK.
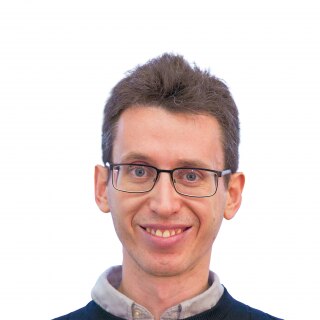
James Myers, Distinguished Engineer, Arm
James leads the devices and circuits team in Arm Research and is an expert in low power design with 20+ patents and 15+ chip tapeouts.
Transcript
Geof Wheelwright: Welcome back to the Arm Viewpoints. We have a great episode lined up for you today. We have two guests that can shed some serious light on the complex world of semiconductor design. And with me today is Scott White CEO of Pragmatic Semiconductor and James Myers, distinguished engineer at Arm. We’ll talk about Arm’s partnership with PragmatIC and their collaboration in designing and manufacturing of flexible chips to solve existing problems and create opportunities for new use cases in an episode we’re calling Beyond Silicon: The Future of Flexible Chips. Perhaps we can start with you, Scott, why don’t you kick us off by telling us a bit more about PragmatIC.
Scott White: We focused on making extremely low-cost flexible electronics. So we’ve developed an entirely new semiconductor manufacturing process that is dramatically lower cost than a conventional Silicon fabrication and in doing so, we end up within an end product that doesn’t involve Silicon. So isn’t the same rigid wafers we’re used to coming out of a Silicon fab, but instead is thin flexible plastic. And that brings
Geof Wheelwright: And that brings us nicely to PragmatIC’s involvement with Arm and we’re joined by a distinguished engineer, James Myers. So Arm and PragmatIC have worked closely for a number of years on researching, designing, and manufacturing flexible chips that address challenges faced by traditional Silicon. Why don’t you begin by explaining what flexible chips are?
James Myers: So flexible chips are non-silicon chips, are they composed of transistors and wires just like Silicon chips but with alternative manufacturing from PragmatIC. The chips you build out of those components look somewhat like Silicon chips from the 1980s, there are tens of thousands of transistors rather than tens of billions that are in our high-end Silicon chips today, they run at somewhat more modest frequencies, the power consumption for operation there hasn’t benefited from 50 years of Moore’s law and so that’s a trade-off there, but they can be flexed physically, they can be integrated into a transparent things and as Scott mentioned, the form factor is very different and they have the opportunity to really be designed bespoke to a particular application.
Geof Wheelwright: So in that context, how did the partnership between PragmatIC and Arm come about?
James Myers: Great story there. So Arm’s CTO at the time Mike Muller, reached out and got in touch with Scott. He then delegated, as all good CTOs do to, to me, go and go and look at the stuff, see what’s there, and whether there is something for us? And I think I first talked to Scott in 2013. So in 2013, when we got together, Scott showed me a way for discrete transistors and a prototype circuit, which was a rectifier, which was driving an LED with some RF energy. So it’s a single transistor circuit which was interesting, but I couldn’t quite scale out in my head to tens of thousands of transistors yet. At six months or nine months later, Scott came back and at that point they had a 10 transistor circuit that had an oscillator, an analog oscillator that could blink an led and from 10 transistors working together in a circuit that I could extrapolate that up to sort of towards 10,000, which we thought we needed as a minimum bar to do a computationally interesting design in this sort of technology. So from there I managed to get to Arm’s original founders actually, who were involved in the very first few Arm chips in the eighties to get onboard and to build a research program around that.
Scott White: And compliment that from our side, as James said, back in 2013, 2014, we were very much at the early stages of a journey, similar to where Silicon was when the Silicon transistor was first invented.
So it was baby steps initially, but it’s showing that we could actually make something. And then the nice thing is we have then a fairly well-trodden path that Silicon has gone through, but we can perhaps move through that path much quicker learning from the experience of the Silicon industry. And so just to build on what James was saying about the key differences between Silicon and flexible chips is in most applications, we’re looking at a different set of use cases from Silicon. This is not about doing a better box of electronics, this is about how you extend the electronics into areas where we wouldn’t normally consider putting it because you have that dramatic difference in cost and form factor and so you can embed it invisibly in things that you wouldn’t normally think of as being an electronic device.
Geof Wheelwright: That’s exciting and I wonder about some of the projects that come out of that? I understand there’s been two big projects that PragmatIC and Arm have collaborated on, the plastic Arm chip and the PlasticArmPit project. Are you able to explain a bit more about those?
James Myers: So the PlasticArm is where we got started. We had this vision. Okay. So we have 10 transistors. Can we call together tens of thousands of transistors and make an Arm processor? When we first started that we had lots of design technology optimization efforts to really understand the limits on both sides. You know, our processor was too big, and we had to cut down our understandings of systems and we had to modify the processor a bit. Although in the end, we were able to make it architecture compliant, it’s not an off the shelf IP product that we had ready. And I remember the first time we simulated a processor implementation, it was sort of the size of it and a full piece of paper. Right, so clearly not viable and over the last eight years we’re down below a square centimeter now in our most recent publication on that project. So that’s amazing and that’s PlasticArm. And then PlasticArmPit sort of evolved from that. There’s a cautionary tale here about temporary project names where that one just stuck and can never be undone, but the PlasticArmPit built on that to say, well, okay, the CPU is still a square centimeter, if we know the application and if we want to really automate a hardened design that just tackles that one thing and is even more optimal and even lower cost, and can overcome some of the technology limitations versus Silicon efficiency per op and so on then how do we do that? How do we transform an armpit sniffing machine learning classifier using high-level Python into a thousand gate, flexible circuit.
Scott White: Yeah and just to add to that, I think the. The interesting things from PragmatIC’s side about both those products is firstly, it’s been useful from our perspective to have something that pushes the boundaries of our technology and makes it and move forward in terms of complexity performance, faster than it would in some of the more commercial applications that we’re deploying volume product into, and at the same time, it’s helped mature the foundry model of working with a designer who is separate from our manufacturing side of things. Similar to the way the Silicon industry has evolved into fabulous designers with foundries that do the manufacturing.
Geof Wheelwright: So it would seem like the partnership that you have and the technology that underpins it has the potential for many different use cases that can redefine a lot of products and industries. But where do you see it having the biggest impact? Are you able to share some examples of where you see it being deployed or any other projects that you’ve done?
Scott White: Sure. So the initial near term focus is around areas related to radio frequency identification (RFID). So RFID is already an extremely high volume markets, about 20 billion RFID tags a year being used for tracking items to improve inventory control and things like that. But with our technology, because it changes that cost point by an order of magnitude, you can extend those same use cases to a much broader range of products where it otherwise wouldn’t make sense. That, although it’s exciting just by itself and there’s a huge opportunity for hundreds of billions to trillions of items just within that one application of RFID, what’s even more interesting is when you start adding sensing and computation into the mix because then you not just have the ability to track those items but you can say something about the environment that they’re in and potentially do some direct analysis of that within the device within the packaging to change something about how it interacts with that environment. So that’s usually the starting point for a lot of the things we’re looking at that crosses over areas like food and beverage. Where being able to monitor supply chain, integrity, freshness of food and so forth within that supply chain, reducing food waste by having a better understanding of how long it’s been in different environments within the supply chain, how long it can really last rather than having a very conservative use by date for example. These are all things that we see as being very exciting applications, not just in terms of the commercial potential, but also in terms of the benefit to the environment and the economy. You can also translate those into things like healthcare, where again, there are some very simple use cases as we’re working on with the NHS around pathology testing. We’re just being able to track the tests in a number of other areas if you can add that sensing and the intelligence of the computation around it then you can start to do much more interesting things like having a smart bandage that monitors your wound as it’s healing or that is monitoring your ECG and heart rate in order to detect things like atrial fibrillation.
James Myers: Like Scott, I’m very interested in new applications of this technology rather than displacing things that silicon can already achieve. But in particular, I’m really excited about contributing to the UN’s development goals. The SDGs, whether it’s by democratized and affordable healthcare like wearable health patches that Scott mentioned that maybe you can just crinkle up and throw away after you’ve used them, to reducing food waste to reducing hunger or smart packaging to improve recycling and optimize resource use and reduce pollution. I’m really passionate about all of those kinds of applications enabled by this kind of center.
Scott White: And that’s very much the same at PragmatIC. In fact, the examples James described crossover very strongly into things we’re directly working with customers and the UK government and other institutions around the world. So for example, we had a project awarded by the UK government a couple of months ago around enabling better recycling and reuse of plastic packaging by using these unique IDs to be able to identify them at the point of disposal and as well as sorting the waste better, you can also provide better consumer incentives for the recycling because it can recognize that somebody has correctly disposed of a product in a way that it can be recycled or reused effectively. But perhaps one interesting thing to build off that which James mentioned the potential here often is around ubiquitous use of these components, which by definition means there’s going to be lots of these things happening, trillions of items a year. And so the sustainability of the product itself and the manufacturing processes is also key in what we’ve been focusing on. So one thing that we’ve been quite pleased about. We can’t claim credit sort of 10 years ago when you started developing the technology of aiming for this, but a natural result of the fact that our processes are much simpler, much more efficient, much lower cost materials than conventional silicon fabs is they’re also much more environmentally friendly. So on a like-for-like basis, we have something like a hundred times lower electricity consumption, a hundred times lower water consumption per circuit, and more like a thousand times lower carbon foot. So that’s sort of where we are already are today and we have some interesting innovations in how we can improve that even further to eliminate certain materials and then there’s certain processes within the manufacturing to actually drive it towards being a net zero carbon neutral manufacturing process for semiconductor devices. So we’re really excited about that and we signed up to programs like Race to Zero for example, with a view that even as we scale our manufacturing to trillions of items within the next decade, getting that to a point of being carbon neutral.
James Myers: So I’m really interested these days in the embodied carbon in electronics, whether it’s flexible electronics from PragmatIC or whether that’s silicon in conventional electronics that may end up in e-waste streams. Very interesting, very complicated set of supply chain analyses needed there. And of course, parts of our ecosystem are doing a lot to again on top of that to understand it and to start publishing data. But I think more needs to be done especially as we move to a circular economy, some of the things we’ve touched on here for circular plastics, Scott was mentioning the recycling packages by tracking them and incentivizing a behaviour change. But I think that needs to move to a lot of different industries beyond just packaging, electronics themselves, our products, if they can be added to a waste stream as some refer to them, but other kinds of products to manage how they flow, how they are reused, how they are recovered, who pays for that and who is incentivized by that. And, so there’s lots of great stuff being done with conventional electronics towards that although we do need to make sure that it is net positive in all cases where we try that but having more options where lower embodied carbon devices can be manufactured and can be designed and can be envisioned, I think really helps the sort of spectrum of circular economy solutions as we move forward. I think it’s a really important set of problems to try and address across all markets and all technologies, whether flexible or silicon.
Geof Wheelwright: I’m intrigued by this idea of the circular economy, maybe you could just talk just a little bit more about what that is and what the impact of that’s going to be?
James Myers: Sure. So circular economy is this idea of rather than a linear economy, where we extract material, we make it into something, we use it, we waste it and then we landfill it. We plan it such that the materials we extract end up looping around, they’re mined, they’re manufactured, they’re used and then they’re repaired first – that’s one loop. They’re reused – that’s another loop, they’re recycled – that’s another loop. And if you can imagine this infinite loop with no loss at the bottom ideally every kilogram of every material we mine; the world, you know, our human economy is irreversibly enriched by that. Clearly that’s a big challenge, that’s a huge mindset change and technology can play a big part there if we’re careful. The World Economic Forum has done some great whitepapers on circular economy approaches to a number of industries in particular. There’s one on plastic packaging and there’s one on consumer electronics as well and the themes within the are the same, a circle as a circle, right. But the cost sensitivity and the lifetime of each kind of product is so different that the actual solutions and the actual ways you’ll bring technology to bear on each of those is quite different. But they have every single buzzwords that our industry is interested in. There’s blockchain, there’s robotics, there’s computer vision, there’s AI there’s cryptography, energy efficiency, material forecasting, and trading and analytics. All of that in this case, for this problem, there are technology pieces everywhere there and all of Arm’s technologies can have a role to play in different bits of those. The interesting one that comes from this work is really bringing the floor down to some of those and really as Scott was saying, enabling lower carbon electronics to be embedded in the smallest and the cheapest of things, because all of our things need to be circular, not just the highest cost ones
Scott White: I think that’s exactly right. That’s the general theme we focus on is that often these kinds of concepts around whether it’s circular economy or anything else, it can be proven in high value products relatively easily, but it’s when you try and extend it to the vast number of things that we interact with or consume on a daily basis and how you actually make that viable economically and actually viable in terms of the sustainability of what you’re adding into the solution in order to help everything else be circular. So that’s sort of the bit that really interests us. If you look at conventional semiconductor manufacturing, for example, it’s perhaps not widely known, that the carbon footprint of semiconductor manufacturing is actually higher than automotive now, which is sort of counter-intuitive to what you’d imagine but it’s basically because of the extended use of electronics in pretty much everything we do in life combined with the increasing complexity of the processes to make them keep up with the vast range of functions we want them to do has just added to that carbon footprint. And so we’re actually not going to go backwards on that front. People will still want that but it’s a case of how do we use that efficiently and how in areas where you can do things in a simpler way. How do we actually make that happen in a way that delivers what we need in a much more efficient way that can create this secularity and sustainability.
Geof Wheelwright: Yeah. And I think you highlight something really interesting there as you bring this vision to life. I’m sure you must’ve encountered many challenges compared with traditional strategies for chip design. Can you talk a little bit about some of the differences and limitations between designing flexible chips and a Silicon?
Scott White: Sure. So, I mean, I can set the scene and then James can probably expand on the design challenges, but just from the capabilities of the technology, I mean, James already mentioned the fact that we started know just a few years ago with one transistor and then 10 transistors. And even now where, you know, we’re sort of in the tens of thousands of transistors which is a lot better, but it’s, it’s kind of where the Silicon industry was say back in the 1980s. Now you could actually do quite a lot in the 1980s, it drove the early PC revolution and we could fly man missions to the moon on a flight controller with just a few thousand transistors in it. So there’s a lot that you can do, but a lot of it requires almost rethinking how we used to approach electronics 30 or 40 years ago rather than building off what we’ve got used to with silicon where you can use billions of transistors and most modern silicon design tends to be focused much more on how do you add functionality, how do you make it more complex, more functional and more, more exciting in that way? A lot of what we’re doing is focused in the opposite direction. How do you create simplicity? how do you take away functions that aren’t needed? How do you just get it back to the bare minimum of what do you need to actually make this application work and effective? and then that really drives it towards something that is deployable, uh, at extremely high volume and extremely low cost
James Myers: The last thing we wanted when we started this program was to go all the way back to design methods from the 1980s. Those are best left in the past and we will not be doing anything manual. We can do things better with the technology we have available to us, the methodology we have available to us, the tools we have available to us than things were done in the eighties, but there’s a bit of effort involved to re-scope and reeducate the tools and to make the most of them for this kind of design.
Scott White: I think I’d just build off that for us it’s always a balancing act between how much do you reuse what is currently being done and how much do you try and intentionally do things differently. From my perspective, and this is the case for every sort of smaller company and probably the most bigger ones as well, it’s about where do you focus your effort innovating and creating new things. And how do you leverage as much of the giants that have gone before you in order to make things effective? So it’s clear
Geof Wheelwright: So it’s clear that you’ve done a lot together and maybe you can talk a little bit about what’s happens next with the Arm and PragmatIC partnership? and maybe talk about some of the initiatives underway now.
Scott White: So there’s probably a range of different things we’re looking at. I think we’re generally less interested in just continuing to push for additional complexity so that the Cortex-M was a sort of key objective there to show that something of that level of complexity can be achieved. But now it’s more about how do you tailor that kind of functionality and focus on specific applications and what is the entire design ecosystem you need to have in place to allow that to happen effectively? The bit that we see as very exciting is the ability to do hardware optimization of our kinds of circuits for individual applications and to be able to do that very quickly, very easily and very low cost.
James Myers: There is no set of application benchmarks for this kind of flexible electronics. We’re blazing a new path here and so we ended up working with partners that have particular expertise in deodorant for the PlasticArmPit project that can give us the use cases and tell us what the constraints are, and maybe mix up a synthetic armpit smell for our sense of partner. And in, in other domains, we’re doing more of this now, you know, we’re working with healthcare experts to understand what do you need from a heart monitor in this sort of flexible patch. And in other places what does a battery company or a battery chemist need from a battery sensor that wraps around the cell. And what can we do with that? If we talk to an automotive company or a UV manufacturer. So all of these different applications, we need to learn a little bit about each to then come back and say, okay, so here is the space we’re in and this is the bit that maps to the most of them, and these are the configurability parameters and so on. So we’re, we’re off at the periphery trying to discover enough to come back to the core and say that’s the IP or the offering.
Geof Wheelwright: That’s exciting. And it gets me to our last wrap up question and asking you both to take out your crystal balls and tell me where you see the technology being deployed in the next five to 10 years. And maybe James, you want to kick us off?
James Myers: Yeah. So I’m a researcher and a bit of a blue sky nerd. So my five to 10, maybe more like 10 to 15, but I really want to see our PlasticArmPit technology deployed in food for reducing waste. You know, food freshness is what I was really excited about. That’s really why I jumped on that project. All the components are the same, but it just needs that, that retraining for that particular application and each kind of food. So proven it but it needs people to embrace and try it out and adapt. So I’m hope I’m hopeful that that sort of thing will be used widely in food in five to 10 years and beyond that.
I’m really excited and I want to see it used in all kinds of sustainable development goal objectives beyond just hunger, you know, also in health care education. I’d really like to see it in circular economy, where other kinds of electronics can help or can’t fit. And beyond that, even further, I want to get, I want to get to biodegradable compute. I think it’s more than 10 years but there are tentative material studies saying that there are potentially ways to build wires and transistors on substrates that will biodegrade. So they could be used then for the more biological half of the circular economy rather than the technical half so you compost the thing down including the computer. I think that would be amazing. I do think that’s more than 10 years off, but I’m very excited about that too.
Scott White: And I think from my perspective actually it’s very similar. So I won’t just repeat it but I think that’s one of the reasons we we’ve actually worked very well together as organizations and as teams is that we have a very similar vision for the types of things that we want to enable with our technology around circular economy, ubiquitous healthcare, and the reduction of food waste and the impact that can have on global poverty and food poverty and so forth. So I think those are the general trends we’re focused on from an application perspective and I guess the other piece which builds a little bit onto the circular economy and carbon footprint is as I said before, this aspiration to actually evolve the manufacturing process even further to make it even more efficient. So for example we’ve actually shown we can eliminate the plastic substrate within our chips, you know, plastics is a bit of a dirty word these days but it turns out that the plastic we’re using our chip is such a small percentage that it’s pretty inconsequential relative to the plastic packaging it’s going on to and if we can improve the recycling of that it has huge leverage, but actually we can improve it even further by, by being able to eliminate certain things within our process or certain material layers and make that even more efficient and environmentally friendly. But I think the high level that I would put within the next five to 10 years from a tangible perspective, other than those specific application areas is just around the ubiquity of deployment of the technology. We’ve set ourselves a goal of being in a minimum of a trillion items within the next decade. And actually, our operational plan is somewhat in excess of that. If you put that into context, the last couple of years is the first time the Silicon industry has manufactured a trillion devices within a year. So that’s after 50 years and we’re aiming to get to that point with our technology within 10. But then I think the other piece that I think is I’m really excited about the more we explore it is the manufacturing model that underpins that being this distributed localized production that avoids very concentrated supply chains, avoid shipping unnecessarily around the world. So within that same timescale we expect to have about a hundred of our fabs deployed in various countries. A lot of them integrated within to our larger customers production facilities in order to actually deliver those trillions of circuits.
Geof Wheelwright: Trillions. I’m just trying to get my head around that. But I really liked the vision you’ve outlined and the fact that it seems very achievable. I’m really looking forward to where this is going to take us in the next decade. And I’m sure our listeners will be watching these developments closely as well. And if you haven’t already do check out the latest edition of Nature to read more about the PlasticArm project between Arm and PragmatIC. That wraps up this episode and we look forward to offering further technology insights in the next episode of Arm Viewpoints. Thanks for listening today.