The ‘Big Four’ in Smart Manufacturing
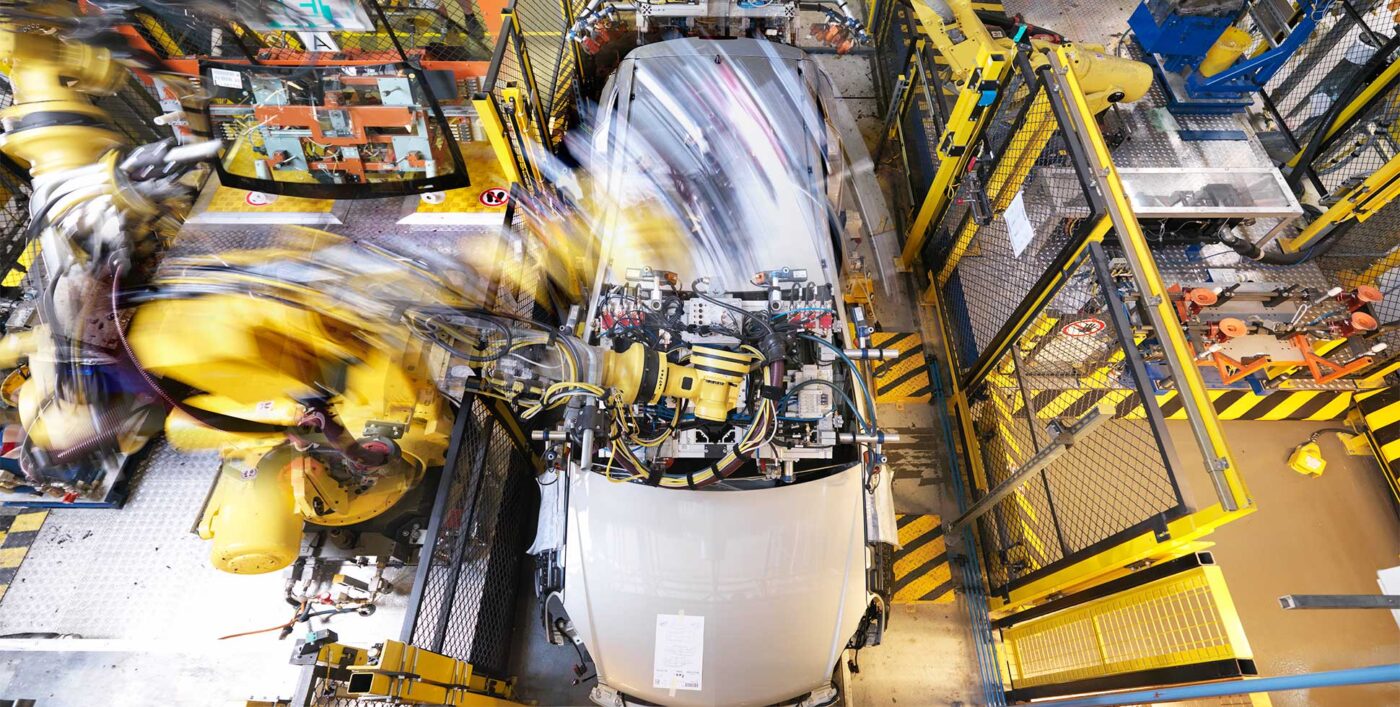
The smart manufacturing vision is growing ever more tangible, driven by a growing array of technology-centric industrial Internet of things (IIoT) solutions to address age-old manufacturing industry challenges.
These smart manufacturing solutions promise a more flexible, efficient manufacturing and supply chain within the IIoT: one that is intelligent, computer-driven, highly adaptable and able to produce multiple products across a single production line without constant retooling.
Exponential growth in this sector is undoubtedly a good thing, offering greater market choice in IIoT devices and pushing down total cost of ownership (TCO). Yet as the IIoT market becomes more saturated, it is likely to become harder for companies to identify whether a solution meets their requirements, now and in the future.
Arm believes that the success of any smart manufacturing solution rests on four fundamentals: performance, real-time capability, security and functional safety.
We call these the ‘Big Four’ because they all play a vital role in the IIoT supply chain of the future. Already, they’re directly influencing advancements made across a wide range of industrial functions, from factory automation to brownfield integration, workload consolidation to robotics. And their role will only grow as smart manufacturing technology advances.
#1: Performance
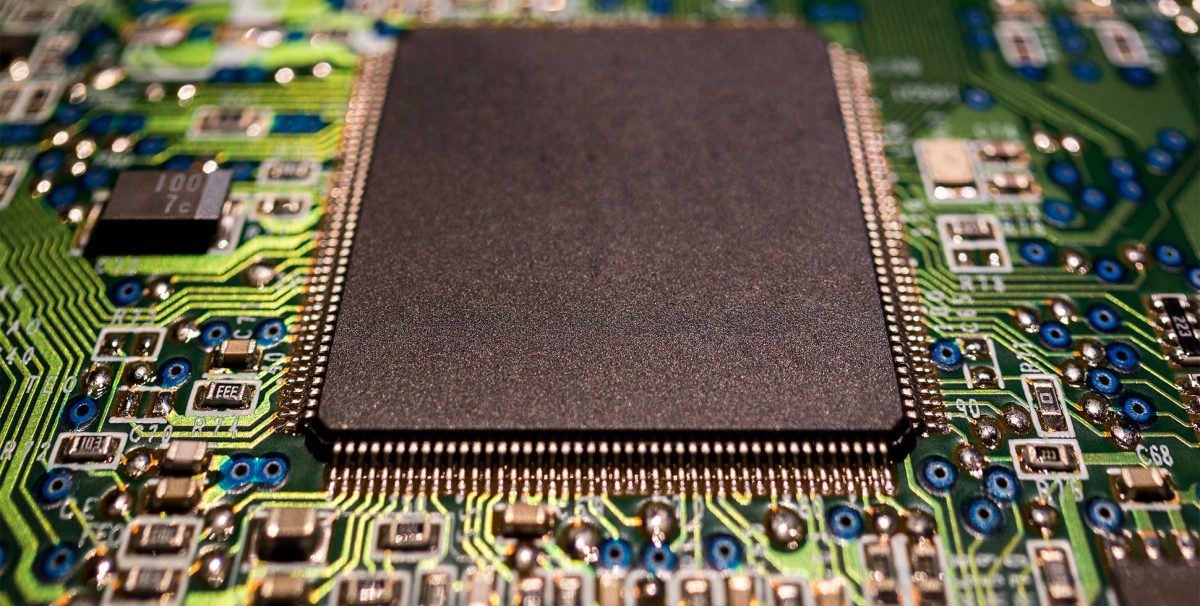
Industrial automation spans a vast array of diverse IIoT devices, from the smallest sensor to the most complex robot. This, in turn, drives a need for the broadest range of compute, with CPUs ranging from ultra-low-power microcontrollers up to high-end server-class processors. Devices may also include GPUs for processing graphics, whether that’s simply driving a touchscreen display or generating complex virtual reality or augmented reality worlds. There’s also the growing requirement for devices to be capable of processing machine learning (ML) workloads, which may take place on the CPU or, for intensive workloads, require a dedicated NPU (neural processing unit).
One key IIoT trend that is becoming abundantly clear is that converging on a single scalable architecture dramatically reduces the overall total cost of ownership. To put this into perspective, many of today’s manufacturing robots are built upon a distributed control system topology. Such functions include the main path planning, safety system, servo drives, security and beyond. Each of these systems is very often based on different CPU architectures, meaning there is very little overlap and reuse within the development cycles, leading to significant engineering investment.
Consolidating these many system types into a single architecture offers a significant reduction in engineering costs whilst bringing benefits throughout the supply chain. The Arm IP portfolio addresses this demand with an architecture that truly scales in performance from the top-to-the-bottom of the industrial automation hierarchy with Cortex-M, Cortex-R and Cortex-A CPUs unlike any other vendor.
#2: Real-time
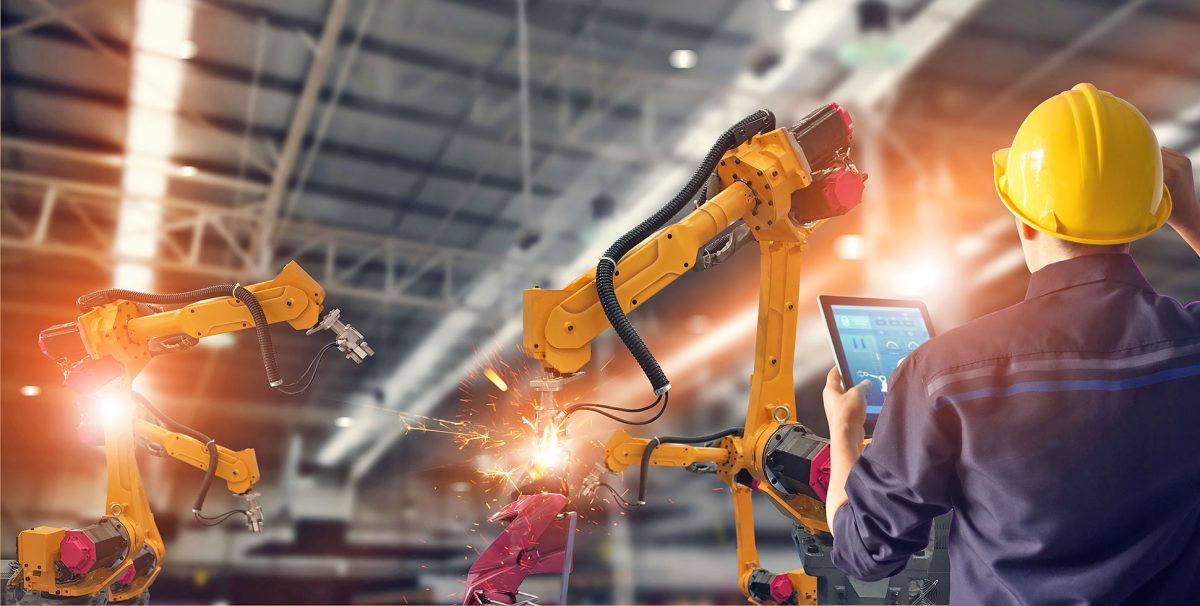
Real-time determinism is critically important within manufacturing. Every production line contains thousands of motors, servos and actuators that must be controlled synchronously during the build cycle of any product. The control of such elements is carried out by devices such as programmable logic controllers, I/O modules and motor drives. The performance of these devices is measured in ‘cycle time’—the number of channels they can control in a given time interval, usually milliseconds or microseconds.
This cycle time naturally places very stringent real-time requirements on the underlying control electronics. These systems must be able to perform their functions in a very deterministic manner without missing a single beat. Imagine, for example, a multi-axis robot welding vehicle bodies on a production line: If the control system misses just a single cycle, the robot arm might not vector to the correct location, a weld would be missed and a potentially dangerous quality issue created.
Real-time performance is vital to many mission-critical smart manufacturing applications and IIoT devices, including the control of autonomous vehicles, industrial robotics and automation equipment—all of which demand immediate and accurate mechanical response. Real-time processors such as the Cortex-R family are designed always to respond within a given timeframe or deadline.
And as applications demand ever-greater compute performance, the need for associated real-time capability is increasing. This is leading to innovation that addresses this fundamental need.
#3: Security
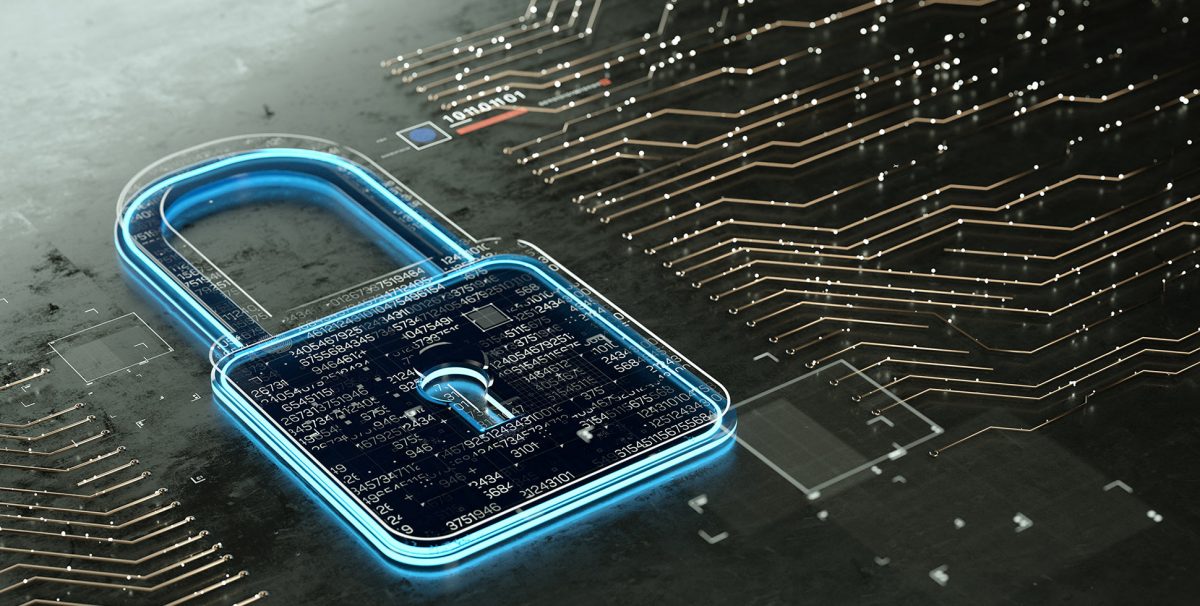
Security touches every point of the smart manufacturing supply chain and is paramount in guarding against a range of vulnerabilities and threat models in industrial systems. Factories need to protect their trade secrets, prevent remote interference to production and also defend products from counterfeiting and cloning. As Operational Technology (OT) and Information Technology (IT) networks begin to merge, there is the potential to expose a greater attack surface outside the factory.
This places additional security requirements on each IIoT device in both the hardware and the software that executes on it. Arm has many assets that enable true end-to-end security including technologies such as TrustZone and CryptoCell which help to reach the minimum security requirements outlined by PSA Certified (co-founded by Arm).
As the IEC62443 industrial automation cybersecurity standard gains momentum, the PSA Certified founders are also invested in mapping the PSA Certified framework to this increasingly important standard that will offer reassurance throughout the supply chain for compliant equipment.
#4: Functional Safety
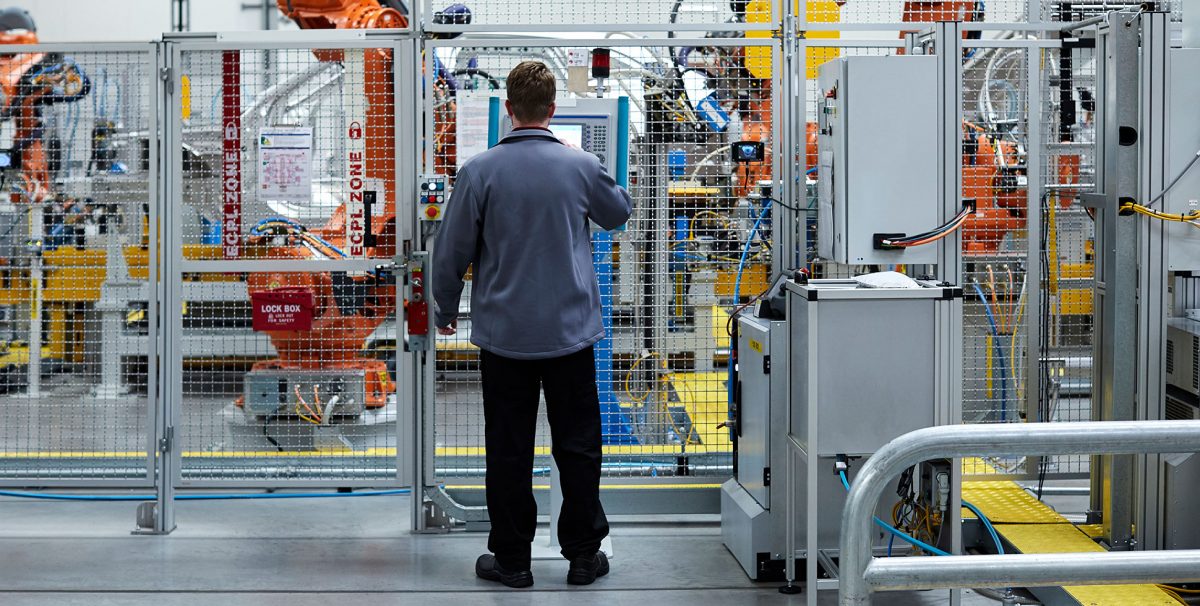
Functional safety is a critical consideration for many systems deployed within a factory, and beyond. It’s the system’s ability to detect, diagnose, and safely mitigate the occurrence of any fault, preventing harm to people and the environment.
Any equipment with integrated functional safety capabilities must adhere to the IEC61508 industrial safety standard. This dictates that systems must function correctly, with potentially unsafe faults detected and controlled to prevent a hazard. Identification of potential failure modes is undertaken through thorough analysis. IEC61508 recognizes two specific types of fault: random and systematic.
Random faults are caused by the unexpected failure of equipment, such as mechanical failure due to wear-and-tear. Systematic failures are those inherent in the equipment’s design, requiring a design change to fix—such as a bug in the device’s software. Any safety-capable equipment must have its compliance certified by Independent assessors before being deployed to the factory floor.
Arm Safety Ready products meet the IEC61508 standard for industrial applications, with supporting collateral available to Arm licensees to build functionally safe devices for the IIoT. This commitment to functional safety supports accelerated development, certification and deployment of safety products.
As the level of automation with the factory increases due to increased productivity and mass customization, so too the pressure to increase the levels of safety. This drives the need for more safety enabled equipment such as programmable logic controllers, robotics systems and motion control.
This is highlighted in the deployment of uncaged robots. Traditionally, the only way to ensure the safe function of robotic mechanisms was to cage them. This was a highly inefficient use of factory floor real estate. However, by implementing key safety technologies, robots could be uncaged, allowing collaborative robots, or “cobots” to work effectively alongside humans on a production line.
This also applies to the emerging autonomous mobile robots being deployed extensively within the factory environment used to efficiently deliver raw materials and sub-assemblies to production stations at the ideal time.
More on Cobots
For more information on this specific use case, read Functional Safety in Industry: Thinking Outside the Cage.
A standardized architecture from top to bottom
Throughout the industrial supply chain, Arm is seeing real appetite for standardizing a single IIoT architecture from top to bottom. This will reduce the total cost of ownership and enable OEMs to truly scale from both a hardware and software perspective.
The ‘Big Four’ are the fundamental IIoT technological prerequisites to ensure smart manufacturing becomes a reality. Arm’s strong background in factory automation enables us to deliver technologies that suit a range of smart manufacturing applications: technologies that offer robust functional safety coupled with proven security technologies and real-time capability.
As a long-standing and committed partner to the manufacturing and industrial sector, Arm continues to listen to and innovate with its silicon partners, OEMs and system integrators to understand evolving market requirements and develop scalable end-to-end solutions that enable the industry to rise to the smart manufacturing challenge.
Read more about Arm’s Industrial solutions.
Any re-use permitted for informational and non-commercial or personal use only.